New Paragraph
The Future of Steel: Advanced AI and Simulation Techniques in Continuous Casting
Exploring Advanced Steel Casting Techniques with Sykora Consulting
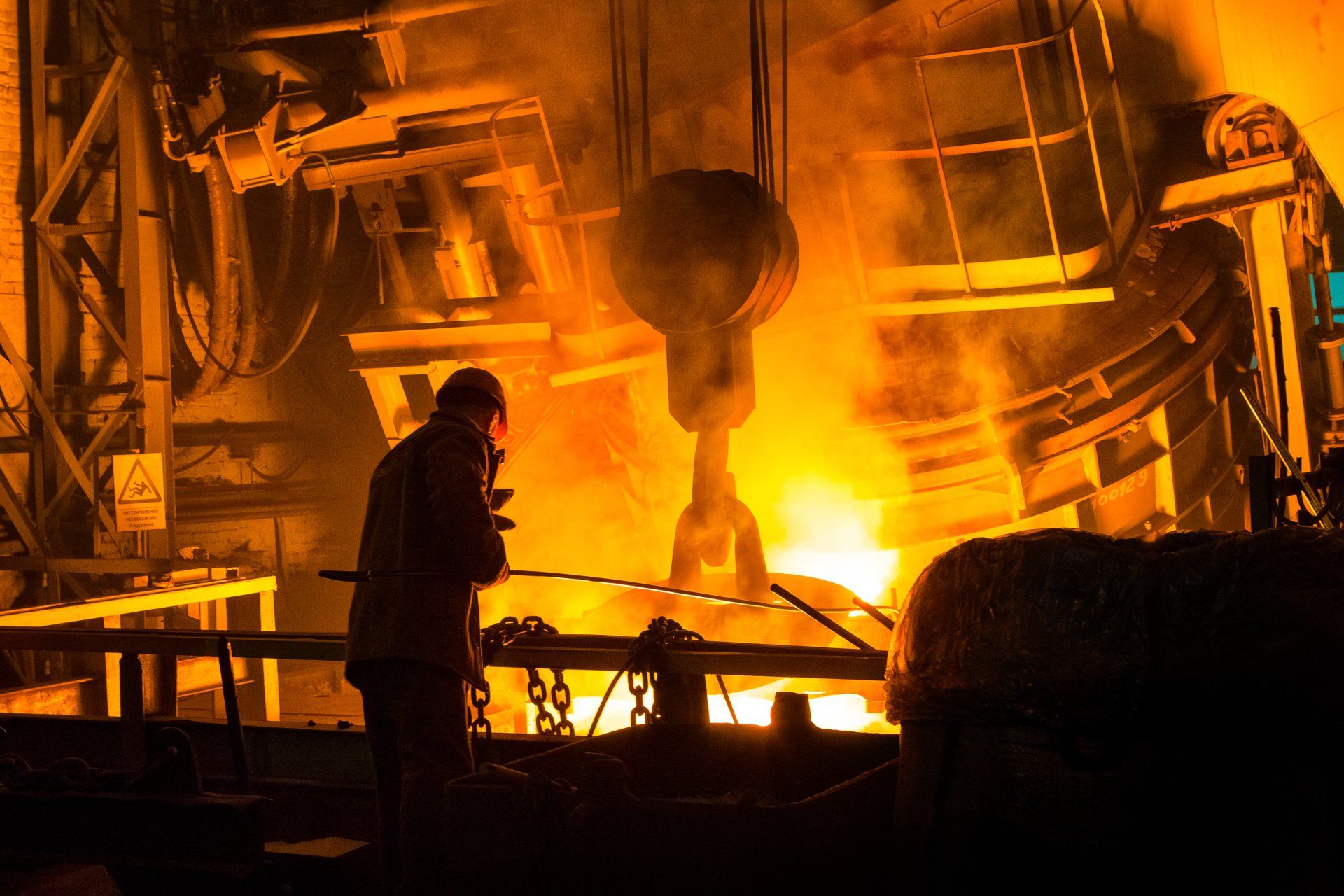
Through intensive research and collaboration with scholars and steel experts worldwide, Sykora Consulting is contributing to the enhancement of cast product quality, boosting productivity, and ensuring strict control over chemistry and cleanliness in the field of continuous steel casting. This is crucial for the smooth functioning of the casting process, which is interconnected with ladle operations and hot rolling. Computational simulations and modeling of the physico-chemical phenomena during casting have been instrumental in addressing industrial challenges and refining process controls.
The formation of defects during casting is influenced by various factors, including steel grade, machine design, and operational parameters. Despite decades of study, a more profound understanding of defect formation and advanced quality prediction methods are essential. This understanding is particularly vital given the recent introduction of innovative steel compositions.
Modern casting machines are equipped with numerous sensors. However, these sensors cannot directly measure the quality of castings, necessitating advanced computerized quality control systems. Traditional quality assessment often relies on comparing real-time process measurements against established standards. While this method is generally effective, it has limitations, especially when defining criteria for new quality specifications or adjusting casting parameters. Advanced quality prediction systems and defect criteria have been developed using sophisticated tools.
Many existing criteria in Steelworks are based on thermo-mechanical calculations, particularly for cracking defects. These models typically suggest that exceeding a certain mechanical strain threshold leads to cracking. However, these models don't always account for the underlying defect mechanisms and obtaining high-temperature mechanical data, including critical strain/stress values, is challenging. Additionally, real-time dynamic methods for calculating stress and strain in continuous casting are in the development.
For hot cracking, some criteria based on solidification modeling have been developed, like the CSC criterion (Cracking susceptibility coefficient). These criteria often consider the solidification interval or the brittle temperature range (BTR), but universally applicable criteria linking defects to specific steel grades or machine conditions are yet to be established. Artificial intelligence-based quality prediction systems have been proposed, but these too don't fully address the mechanisms of defect formation.
There's a clear need for higher-level, science-based fundamental models that can simulate key phenomena in continuous casting and their relation to defect formation. Such computational models are crucial for understanding defects and could be integrated into online quality prediction systems, offering insights into defect types and practical solutions.
Our research in cooperation with many Universities around the globe and our consultancy experience is dedicated to establishing new quality criteria for automated control systems in the continuous casting process, leveraging advanced computational tools. A key component of our initiative is the use of a Multiphysics microstructure simulation tools, designed to replicate microstructural phenomena during key stages such as solidification, cooling, and reheating. This comprehensive approach encompasses the entire spectrum of processes from casting to hot rolling.
To accurately assess the impact of varying cooling patterns on product quality, this simulation tool is typically integrated with both online and offline heat transfer models. These models, known for their rapid processing capabilities, are grounded in fundamental phenomena, rendering them highly effective for application in steel manufacturing facilities.
The effectiveness of these simulation tools is further enhanced when combined with Artificial Intelligence (AI) technologies. The integration of AI with simulation tools has shown immense potential in improving quality by utilizing diverse data sets and various predictive AI models. This synergy allows for a more nuanced and precise analysis, leading to the development of robust quality criteria.
The determination of defect formation in the casting process is a complex task, relying on the cumulative effect of multiple quality criteria. These criteria are informed by a combination of models and data that describe the mechanical and thermal stresses involved in the process. The tools and methodologies developed in our research and are based on our long-term expertise, along with the newly established quality criteria, are focused on addressing different types of cracks and gas defects. The use of simulation tools in tandem with AI technologies demonstrates a significant advancement in the field, offering more accurate predictions and insights into defect formation, ultimately leading to enhanced quality control in steel production.